人工砂石生產(chǎn)線的產(chǎn)品主要作為混凝土骨料使用,而為了保證混凝土的強(qiáng)度、和易性等要求,混凝土骨料有著嚴(yán)格的行業(yè)標(biāo)準(zhǔn)。這就要求我們在生產(chǎn)過程中對產(chǎn)品質(zhì)量進(jìn)行嚴(yán)格的控制。
第三部分 粗骨料的超遜徑控制
破碎、分離和混料是引起骨料超遜徑的主要原因。
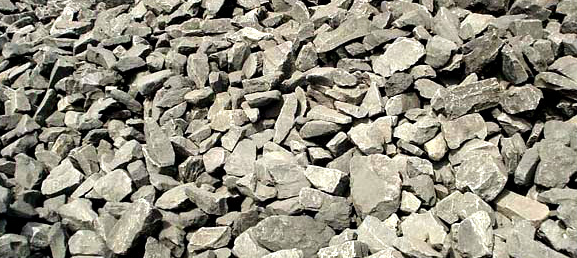
(1)成品骨料從篩分樓出來后,還要經(jīng)過多次轉(zhuǎn)運(yùn)緩解才能夠進(jìn)入攪拌機(jī)。即使是非常堅(jiān)硬的巖石,轉(zhuǎn)運(yùn)破碎也在所難免。對于硬度較低、含有裂隙和脆性的骨料,二次破碎就更加明顯,有的石塊由于碰撞而破裂成幾塊,有的在輾轉(zhuǎn)研磨中棱角剝落,表面磨光,自身粒徑減小成為遜徑料,并產(chǎn)生了石屑和石粉。
減小破碎的簡單而有效的方法是簡化砂石加工系統(tǒng)生產(chǎn)工藝,減少轉(zhuǎn)運(yùn)環(huán)節(jié)。此外,在工藝設(shè)計(jì)和生產(chǎn)中還要采取下列措施:
1)在一切轉(zhuǎn)運(yùn)環(huán)節(jié)都要盡量減少骨料自由降落高度,避免骨料急劇改向和堅(jiān)硬物件的直接碰撞。
2)如果卸料點(diǎn)是固定的,則自由落差超過5m時(shí),大、中石一般要設(shè)緩降器,以便讓骨料多次轉(zhuǎn)折或沿斜面滑下,降低碰撞速度,減少破裂。隨著碰撞次數(shù)增加,碾轉(zhuǎn)研磨的作用增強(qiáng),剝落型的破碎和骨料分離可能會有所惡化。
3)生產(chǎn)中不宜將儲倉和碎料場內(nèi)的骨料卸空后再裝料,一面自落高度過大或直接撞擊倉壁會引起物料破碎。骨料通過溜槽進(jìn)入皮帶機(jī)和其他設(shè)備時(shí),應(yīng)力求物料和運(yùn)動方向一致,避免急劇改變流向和石料間相互碰撞。如果料塊較大而又夾有細(xì)料,則可在進(jìn)料槽底部開些小孔,以便細(xì)料先漏下作為鋪底,形成一個(gè)緩沖的底層,這樣即保護(hù)了膠帶,又減少了破碎。
4)二次篩分時(shí),采用孔徑略大的篩網(wǎng),有意識地增多超徑石含量,以補(bǔ)償由于破碎引起的大顆粒含量的減少。
(2)一個(gè)粒徑級的骨料,在堆存和轉(zhuǎn)運(yùn)過程中,保持粗細(xì)料分布均勻,避免分離是不易的。例如,皮帶機(jī)卸料時(shí),粗骨料一般拋的比較遠(yuǎn),細(xì)骨料拋得近;骨料沿溜槽或錐形斜面滾落時(shí),粗料的滾動速度大,常先滾到坡腳,細(xì)料的阻力大、速度慢,落在粗料的后面或停留在坡頂。減少骨料分離應(yīng)采取下列措施:
1)中心落料。無論是從皮帶機(jī)機(jī)頭拋料還是溜槽滾落,都要求把料集中到一個(gè)漏口并有一端豎直的溜管,以保證骨料從中心豎直下落。
2)盡量采用成層堆放料,避免一次堆成圓錐形。
3)如果從地弄取料,最好同時(shí)從幾個(gè)(如3個(gè)以上)料口取料。這樣分離了的粒徑也因同時(shí)取料而得到補(bǔ)償。
(3)混料主要由于擋墻、料倉分隔不好,溜槽、篩網(wǎng)損壞,運(yùn)載工具和料倉卸料清倉不干凈而引起。減少混料可采取下列措施:
1)日常做好設(shè)備和設(shè)施的維護(hù)工作,避免發(fā)生混料。
2)各級骨料倉應(yīng)設(shè)置隔料墻,隔料墻應(yīng)有足夠的高度和強(qiáng)度,并應(yīng)避開強(qiáng)風(fēng)。
3)避免泥土和其他雜物混入骨料中。